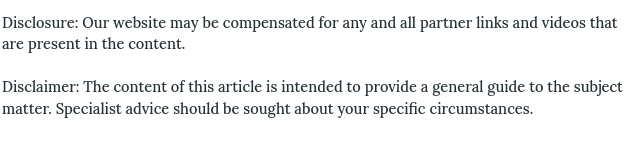

While younger Americans may not remember the major environmental disasters of the 1970s and 1980s, older adults are grateful for recent advances in composite engineering. Chernobyl, Bhopal, and Three Mile Island all made the news many years ago for the large-scale environmental disasters that occurred there. Engineers have been working on composite materials that provide protection against corrosion, explosion, and leakage. Composite materials are also being tested for their inclusion in new homes built to withstand tornadoes: there is one art museum that has been testing composite fiberglass tubes that are impervious to corrosion and that can withstand winds of more than 150 mph.
Composite engineering is not exactly a new idea, but the widespread implementation of composites as building materials is still relatively new. In the early 1950s, the Corvette was made with composite engineering materials, and the cars have survived at much higher rates than their competitors. There were experiments done in the 1960s where health officials buried a gas tank that was made with composite materials. Recently, it was unearthed and was found to be in pristine condition. There were no industrial leaks, no corrosion, and public health officials determined that the tank would have been fine underground for at least 20 more years – advanced composites are making headway.
There has also been a movement to renovate bridges with FRP decks, a term that means “fiberglass reinforced plastic.” America’s bridges are aging at an alarming rate, and there are many metropolitan areas that cannot afford to stop or reroute traffic for extended periods of time. There have been several videos on social media channels documenting bridges at the exact moment of their collapse, and contractors as moving toward fiberglass and plastic as viable building and renovation materials. Composite engineering has been tested on bridges out on the west coast, and more smaller towns are following suit.
Composite manufacturing and composite molding are also influencing astronauts’ experiences in space: NASA is in the process of testing a fuel tank that would be used on long-term, “deep space” missions. Space expeditions require using fuel tanks that have a very large capacity, but that are extremely lightweight. Space travel experts are currently testing a fuel tank made from composite materials that would save 25% in the initial cost of rocket launching and are also testing other radiation shielding materials.
Composite materials are extremely resistant to rust and corrosion, and the American food service industry has started to incorporate fiberglass reinforcements into production facilities. Manufacturers around the world are also making the switch to composite materials for hazardous work environments. In the next several decades, we should expect to see homes that are completely immune to wind and water damage from tornados and hurricanes, as home builders improve on industrial composite technology.