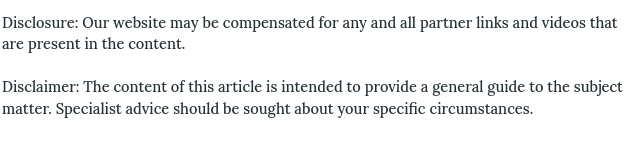

It is hard to believe that prior to the invention of CT scanning services in 1972, the only way for a doctor to get a full picture of the inside of a patient was to physically open them up and look. As you can imagine, this often harmed the patient more than the information gathered from the invasive diagnostic procedures provided. For this reason, when Godfrey Hounsfield and Allen Cormack had the bright idea to compile hundreds of 2D x-rays to create 3D imaging of the inside of a patient without laying a scalpel on them, it utterly shook the way physicians conducted tests for diagnostic purposes. The discovery had such a big impact on humankind that the inventors were eventually awarded Nobel Peace Prizes for their contribution to Science.
Meanwhile, the industrial manufacturing sector still faces the same dilemma that the medical world had prior to 1972. Testing of parts is a critical piece of manufacturing, but contemporary processes are costly, time and labor intensive, and often destroy the part in the process. While many engineers and manufacturers live under this constant struggle, the exact same 3D scanning services that are used in the medical sector could be easily transferred to the industrial sector. This would allow manufacturers to quickly gather vital part information, both inside and out, without a finger being laid on the part itself. Let’s consider a few ground-breaking ways that industrial CT scanning inspection services are starting to be used:
- Reverse Engineering
There are several reasons that reverse engineering is a critical part of the industrial sector. When a critical part in the manufacturing equipment is damaged and no longer being produced, the entire assembly line is put on hold until a new solution can be found. Other important functions of reverse engineering include instances where a manufacturer needs plans for a part that they didn’t produce themselves.
CT scanning tomography makes reverse engineering easier than ever. The original part is scanned in all angles, and a 3D image is created of the inside and out of it. That image can be used to develop plans to create an exact replica of the part, without any damage coming to the original part itself.
- First Article Inspections
When a manufacturer creates a product for a client, the client often wants to ensure the quality of the product before the assembly line cranks up and produces several hundred (or thousands) of them. Using CT scanning tomography, every angle and aspect of the product can be inspected and tested almost instantly. This includes:- Part to CAD comparisons. This process identifies any deviations from the original CAD plans.
- Part to part comparisons. This ensure consistency throughout the manufacturing process.
- Wall thickness analysis/ This test involves exact measurements being taken of the part, and the inner void considered to calculate the thickness of the walls to ensure quality.
- Fiber analysis. Fiber analysis ensures that accuracy and quality in the part down to the deepest detail.
- Rapid Prototyping
When a scale model of a prototype needs to be developed quickly, CT scanning technology can be used to quickly develop CAD plans. These CAD plans can easily be created with a 3D printer. The time it takes to go from concept to prototype is days (or less), when the development process would have taken far longer prior to the use of CT scan technology in manufacturing. - Assembly Analysis
Assembly analysis is used to stress test a part and analyse how several components work together to ensure quality. Basically, a 3D image is captured of the inside and out of a part (or several parts), and then a computer animation of the parts working together is created. This allows manufacturers to get a detailed analysis of how the part or system work together and identify any flaws before they actually fail in real life.
In a world where we expect everything instantly, it is incredible how cumbersome and slow contemporary part testing methods are, and how long it has taken for CT scanning equipment to hit the industrial sector. However, as it makes part testing and inspection easier, cheaper, and faster, it is becoming the industry standard.